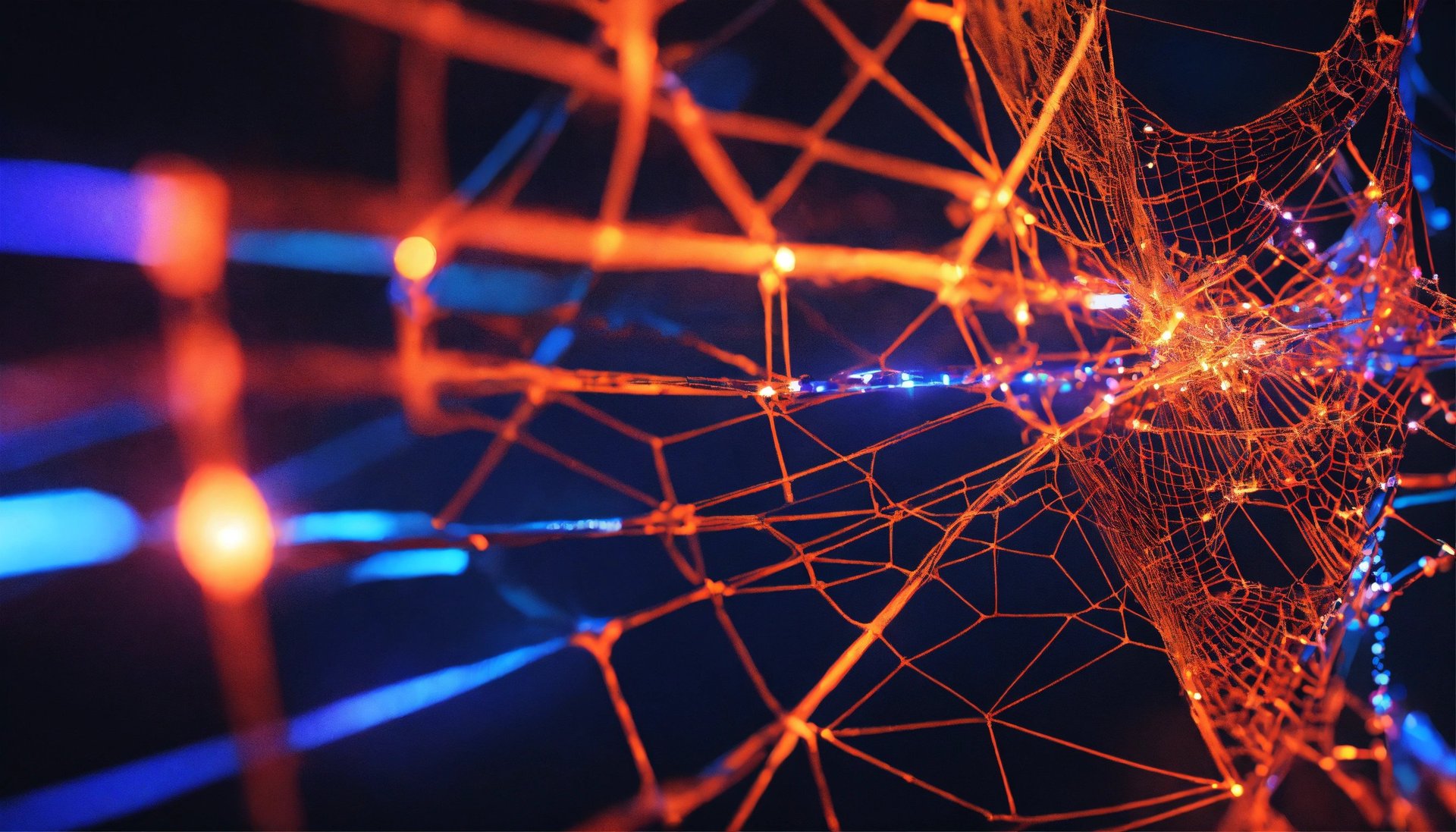
Revolutionizing the Skies: Transforming Aviation Supply Chains with Digital Twins Technology
Discover how digital twins technology is revolutionizing the aviation industry by transforming supply chains. Learn how this cutting-edge innovation is streamlining processes, improving efficiency, and reducing costs in the skies.
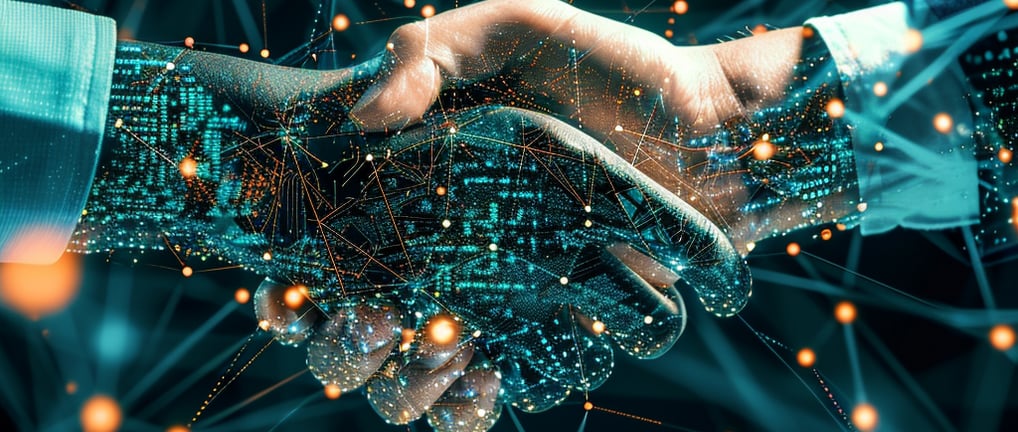
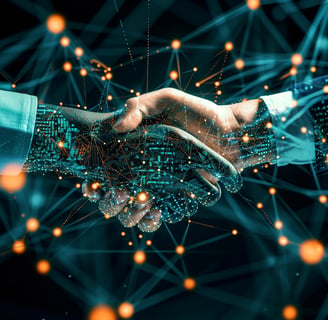
Introduction
Aviation supply chain management, an intricate network encompassing production, distribution, and logistics within the aviation industry, plays a critical role in ensuring the smooth operation of airlines, aircraft manufacturers, and related entities. The aviation sector is an ever-evolving industry that constantly seeks innovations to boost efficiency, reduce costs, and enhance safety standards. With the global aviation market projected to witness rapid growth, the demand for robust supply chain management practices is more pressing than ever before (Statista, 2021).
In recent years, the advent of digital twins has emerged as a revolutionary technology with the potential to transform the aviation supply chain landscape. Digital twins, virtual replicas of physical assets or systems, are equipped with real-time data and simulations that enable stakeholders to monitor, analyze, and optimize various facets of operations. By harnessing the power of digital twins, aviation companies can gain valuable insights into their supply chains, predict maintenance needs, and streamline processes for improved performance and competitiveness in the market (Deloitte, 2020).
The Evolution of Aviation Supply Chain Management
The aviation industry has witnessed a significant transformation in its supply chain management practices over the years. With the increasing complexity of global networks, the focus has shifted towards creating more agile and responsive supply chains to meet the demands of the market efficiently. The evolution of aviation supply chain management can be attributed to advancements in technology, changing customer expectations, and the need for greater sustainability within the industry.
Furthermore, the adoption of just-in-time inventory systems, lean manufacturing principles, and collaborative partnerships with suppliers has played a pivotal role in streamlining supply chain operations in the aviation sector. This evolution has resulted in improved inventory management, faster response times to market changes, and enhanced overall efficiency in the delivery of critical components and parts for aircraft manufacturing and maintenance processes (Whyte, 2019).
Introducing Digital Twins: A Game-Changer for Aviation
Digital twins are revolutionizing the aviation industry by leveraging cutting-edge technologies like AI to create virtual replicas of physical assets. These digital replicas enable companies to monitor, analyze, and optimize their operations in real time, leading to significant improvements in efficiency and cost savings. By harnessing the power of AI, digital twins can predict maintenance needs, identify potential issues before they occur, and streamline decision-making processes for better overall performance.
In a rapidly evolving industry where downtime can have costly implications, digital twins offer a game-changing solution for enhancing operational resilience. By providing a comprehensive view of an aircraft's components and systems, companies can proactively address maintenance issues, optimize performance, and ensure aircraft safety. The integration of AI in digital twins transforms data into actionable insights, empowering aviation companies to make informed decisions that drive productivity and competitiveness in today's dynamic market.
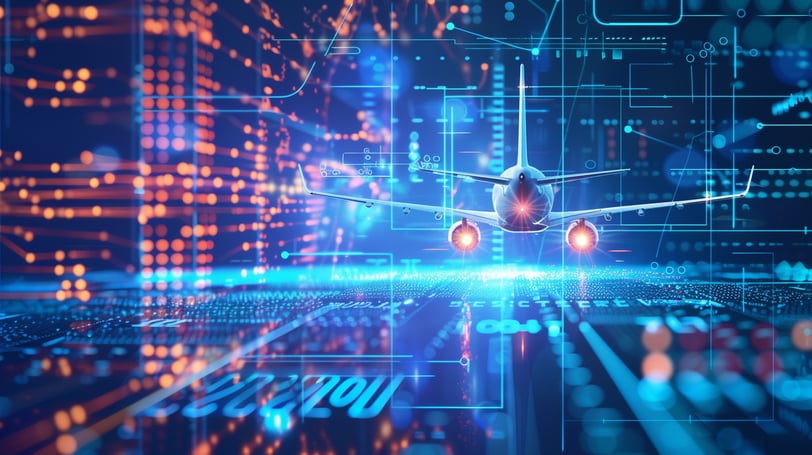
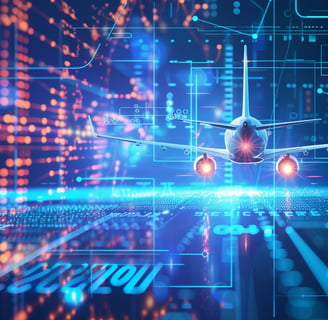
Understanding Digital Twins Technology
Digital twins represent a cutting-edge technology that has revolutionized the way industries such as aviation manage their operations. In the realm of aviation, digital twins are virtual representations of physical aircraft, engines, systems, or components. These virtual models are created through the integration of various real-time data sources, allowing for a comprehensive and accurate depiction of the actual assets. From monitoring performance to predicting maintenance needs, digital twins offer a holistic view that enables proactive decision-making and optimization of aviation processes.
The use of digital twins in aviation has significantly enhanced predictive maintenance capabilities, enabling operators to identify potential issues before they escalate, thus reducing downtime and enhancing overall efficiency. By simulating various scenarios and conditions, digital twins allow for the testing of different maintenance strategies without impacting actual operations. This proactive approach not only minimizes disruptions but also contributes to cost savings and improved safety standards in the aviation supply chain.
Defining Digital Twins in the Context of Aviation
Digital twins in aviation refer to virtual replicas of physical aircraft assets, engines, or systems. These virtual models are created using real-time data collected by sensors installed on the physical equipment. The idea behind digital twins is to enable a comprehensive understanding and analysis of an aircraft's performance, maintenance needs, and operational efficiency. By harnessing the power of data analytics and simulation, aviation companies can propel their operations into a new era of predictive maintenance and enhanced decision-making. This transformative approach has the potential to revolutionize how the aviation industry manages its assets, leading to improved safety, increased reliability, and cost savings.
The concept of digital twins has gained significant traction in recent years, with major aircraft manufacturers and operators investing heavily in this technology. For example, General Electric has been a pioneer in adopting digital twins for their aircraft engines, allowing them to monitor performance, predict maintenance issues, and optimize operations proactively. By creating a digital replica that mirrors the behavior of the physical engine in real time, GE Aviation has been able to achieve impressive results in terms of reducing downtime, enhancing reliability, and extending the lifespan of their engines. This concrete evidence showcases the tangible benefits of integrating digital twins into aviation supply chain management, setting a new standard for operational excellence in the industry.
How Digital Twins Work: Components and Processes
Digital twins in aviation entail a sophisticated interplay of digital components and processes that mirror physical assets and operations with an unprecedented level of accuracy. At the core of digital twins technology lie three key components: sensors, connectivity, and analytics. Sensors gather real-time data from aircraft components, infrastructure, and subsystems, while connectivity enables seamless communication between these components and centralized systems. Analytics processes the vast data streams produced by sensors to generate actionable insights and predictions. This synergy of components forms the foundation of digital twins, enabling organizations to monitor, simulate, and optimize aircraft operations in near real-time.
Furthermore, the processes involved in digital twins are intricately designed to enhance operational agility and decision-making in aviation supply chains. By continuously collecting data from physical assets, digital twins create a virtual representation that simulates operational scenarios and identifies potential issues before they manifest. This predictive capability allows aviation companies to proactively address maintenance needs, optimize routes, and streamline logistical operations. Ultimately, the seamless integration of components and processes in digital twins revolutionizes how aviation stakeholders manage their assets and resources, paving the way for greater efficiency and competitiveness in a dynamic industry.
The Impact of Digital Twins on Aviation Supply Chains
In the aviation industry, the implementation of digital twins has significantly transformed supply chain management processes. By leveraging advanced technologies like IoT sensors and big data analytics, digital twins offer real-time insights into aircraft components, enabling maintenance teams to predict potential issues before they occur. This proactive approach helps airlines streamline their operations and reduce unplanned maintenance downtime, ultimately enhancing overall fleet performance.
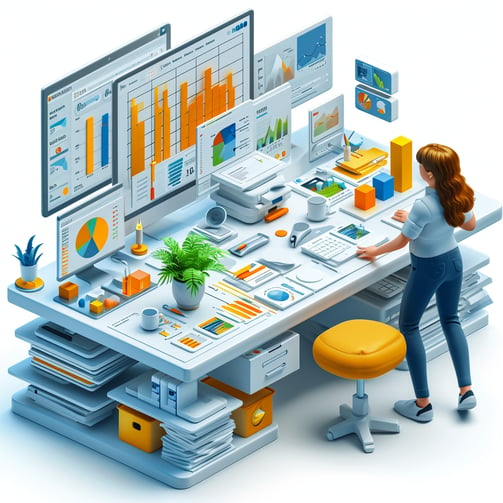
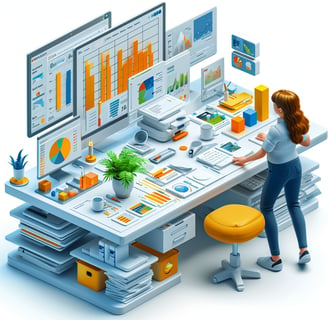
Furthermore, digital twins facilitate data-driven decision-making by providing accurate simulations of aircraft behavior and performance. Through predictive maintenance algorithms, operators can optimize maintenance schedules, extend the lifespan of critical components, and ensure regulatory compliance. According to a study by MarketsandMarkets, the global market for digital twins in aviation is projected to reach $3.4 billion by 2025, underscoring the industry's growing reliance on these innovative technologies.
Enhancing Efficiency and Transparency
Digital twins are revolutionizing the aviation industry by enhancing operational efficiency and transparency. By creating virtual replicas of physical assets, manufacturers can monitor performance in real-time, predict maintenance needs, and streamline supply chain processes. This technology enables stakeholders to make data-driven decisions, optimize resource utilization, and minimize downtime, ultimately leading to significant cost savings.
Through digital twins, companies like Rolls-Royce have seen a 20% reduction in engine maintenance costs and a 40% decrease in unplanned downtime. This level of operational efficiency is crucial in an industry where every minute an aircraft is grounded results in substantial financial losses. By leveraging digital twins, aviation companies can proactively address maintenance issues, improve asset reliability, and ensure smoother operations throughout the supply chain.
Reducing Costs and Downtime
As aviation supply chains grapple with the continuous pressure to optimize costs and minimize downtime, the integration of digital twins presents a compelling solution. By leveraging real-time data and predictive analytics, companies can proactively address maintenance needs, thus reducing unexpected disruptions and associated costs. According to a report by Market Research Future, the adoption of digital twin technology in the aerospace industry is projected to grow at a CAGR of 16% between 2020 and 2027.
Furthermore, digital twins enable precise monitoring of various components within an aircraft, allowing for timely interventions and preventive maintenance measures. By identifying potential issues before they escalate, airlines can avoid costly downtimes and maximize the operational efficiency of their fleets. For instance, General Electric Aviation has successfully used digital twins to optimize engine performance, resulting in significant reductions in maintenance costs and unplanned maintenance events.
Case Studies: Digital Twins in Action
Today, digital twin technology is revolutionizing the aviation industry by offering enhanced predictive maintenance capabilities and optimizing aircraft performance. One noteworthy case study that highlights the impact of digital twins in action is Rolls-Royce's adoption of this innovative technology for their aircraft engines. By creating digital twins of their engines, Rolls-Royce has been able to monitor real-time data and predict maintenance needs proactively, leading to a significant reduction in maintenance costs and downtime for their fleet. This implementation has not only improved operational efficiency but has also ensured maximum safety and reliability for their aircrafts. Reference: https://www.rolls-royce.com/innovation/digital/digital-twin.aspx
Another compelling case study showcasing the power of digital twins in aviation is Boeing's utilization of this technology in aircraft design and manufacturing processes. Through the use of digital twins, Boeing has successfully simulated various scenarios and conducted virtual testing to optimize aircraft structures and systems. This approach has enabled Boeing to streamline their production processes, reduce errors, and enhance overall quality control. As a result, Boeing has been able to deliver cutting-edge aircraft designs to their customers while significantly reducing time-to-market and production costs. Reference: https://www.hannovermesse.de/en/news/news-articles/boeing-aims-to-virtualize-the-development-of-aircraft
What is a digital twin?
A digital twin is a virtual representation of a physical object or system, used to simulate, monitor, and analyze its real-world counterpart.
How are digital twins utilized in the aviation industry?
In the aviation industry, digital twins are used to model and optimize various aspects of aircraft and supply chain management, leading to improved efficiency and cost savings.
Can you provide examples of how digital twins have been applied in aviation supply chain management?
Yes, digital twins have been used to track and monitor the performance of aircraft components, predict maintenance needs, and optimize inventory levels in the aviation supply chain.
What benefits do digital twins offer to the aviation industry?
Digital twins in aviation can enhance efficiency and transparency, reduce costs and downtime, and improve overall operational performance.
How do digital twins work in the context of aviation?
Digital twins in aviation consist of various components such as data collection sensors, analytics software, and visualization tools that work together to create a dynamic, real-time model of aircraft and supply chain operations.
About the Author:
Waqar Jadoon, with 28 years in aviation supply chain management, holds an MBA and a software engineering degree. Renowned for streamlining operations and integrating AI and data analytics, he blends technical and business expertise to drive industry innovation. Waqar champions sustainable practices and technological advancements, shaping the future of aviation logistics.